Table of Contents
In industrial settings, the effectiveness of preventive maintenance is greatly enhanced by the use of Computerized Maintenance Management System (CMMS) software, which raises uptime and lowers expenses.
1. Introduction to Preventive Maintenance
By routinely inspecting and maintaining tools, systems, and machinery, preventive maintenance takes a proactive approach to preventing equipment failures. Conventional techniques were labor-intensive and prone to mistakes. More accurate interventions are made possible by the automation of scheduling, documentation, and monitoring tasks by modern technology, especially CMMS software. By taking care of possible problems before they become serious enough to require expensive repairs, this method can lower downtime, increase equipment life, and save money.
2. What is CMMS Software?
Software that manages work orders, keeps track of schedules, and keeps an eye on equipment performance is called a Computerized Maintenance Management System (CMMS). It automates preventive maintenance procedures by storing comprehensive data about machinery. To spot patterns, foresee problems, and make wise decisions, CMMS offers analytics and reporting. Increased operational effectiveness, decreased downtime, longer equipment lifespan, and financial savings from manual tracking and postponed maintenance are the objectives.
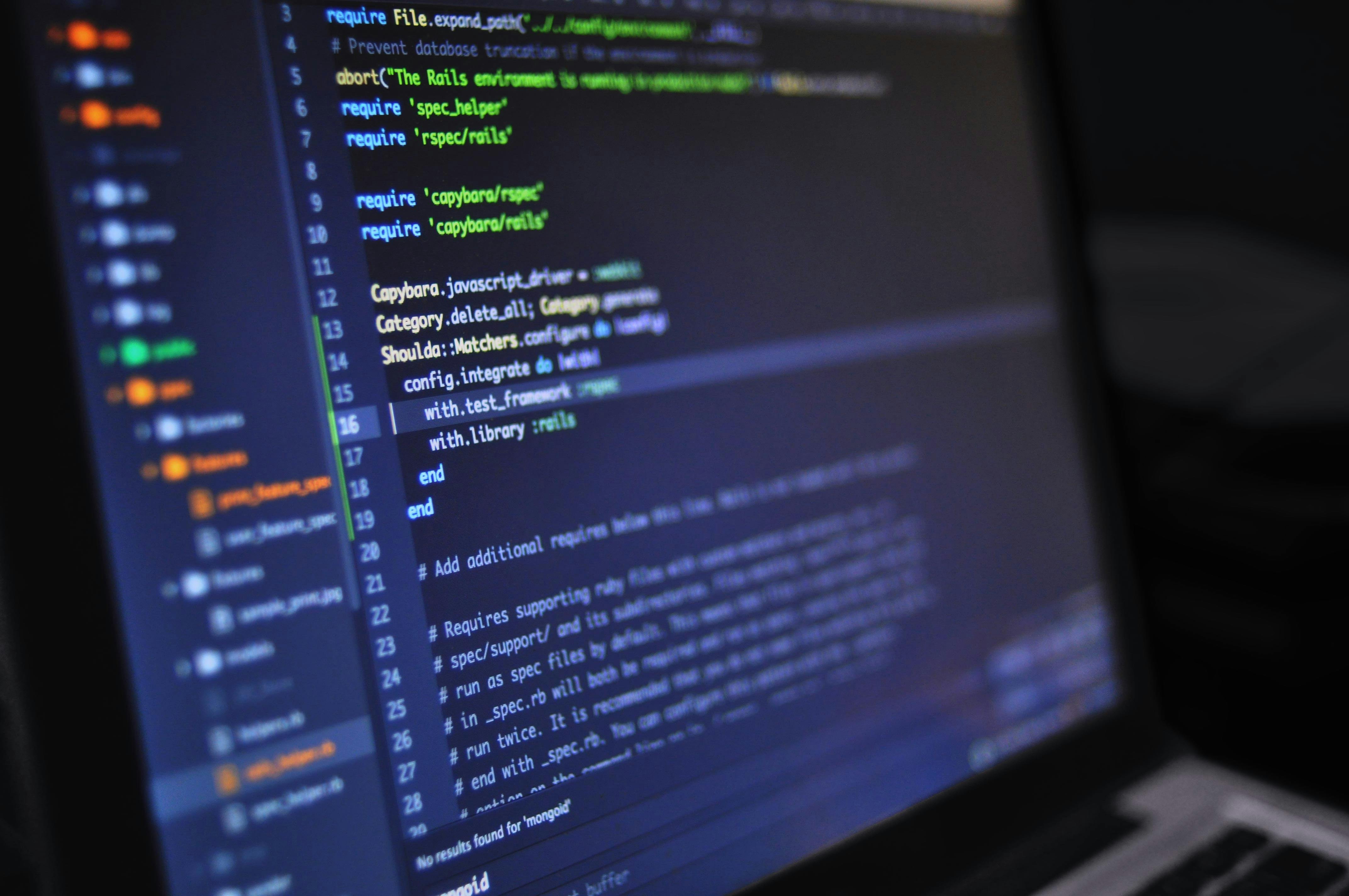
3. The Importance of Preventive Maintenance
For businesses that depend on machinery and equipment to function, preventive maintenance is crucial. The decrease in unplanned breakdowns is one of the primary benefits. Regular maintenance helps businesses spot wear and tear early on, avoiding expensive malfunctions and unscheduled downtime. Additionally, by ensuring that all equipment functions properly and lowering the chance of accidents, preventive maintenance contributes to increased safety. Because proactive maintenance extends the operational lifespan of machinery and reduces emergency repair costs, it is more economical than reactive repairs. Over time, these regular preventive measures promote more efficient workflows, increased output, and increased trust in the dependability of the equipment.
4. How CMMS Enhances Preventive Maintenance
By automating crucial tasks, CMMS software significantly increases the efficacy of preventive maintenance. The ability to plan maintenance tasks according to usage patterns, time intervals, or condition monitoring is one important feature. This guarantees that maintenance chores are completed on a regular basis without relying on human memory or effort. Additionally, technicians can receive real-time notifications and reminders from CMMS regarding impending or past-due maintenance tasks. Additionally, it makes it possible to track every maintenance task in detail, providing information about the equipment’s condition and history. Better planning and resource allocation are made possible by this predictive capability, which eventually results in more effective maintenance procedures and lowers the chance of unplanned breakdowns.
5. Benefits of Using CMMS Software
There are many advantages for businesses that use CMMS software. First of all, it guarantees that preventive maintenance activities are planned and carried out in a methodical manner, which drastically cuts downtime. Second, by guaranteeing that equipment is maintained correctly and on schedule, CMMS extends the life of assets. By prolonging the equipment’s useful life and averting significant malfunctions, this software also lowers maintenance expenses. Improved compliance is yet another important benefit; CMMS makes sure that maintenance operations follow rules and guidelines set forth by the industry. Furthermore, it facilitates improved resource management by offering information on technician workloads and inventory levels. All things considered, CMMS software facilitates a more proactive, well-organized, and efficient maintenance workflow, increasing output and lowering costs.
6. Real-Time Monitoring and Reporting
The real-time monitoring and reporting capabilities of CMMS software are among its most notable features. CMMS gives current information on the condition and health of assets by continuously monitoring equipment performance and maintenance activities. Managers can swiftly make well-informed decisions and resolve problems before they worsen thanks to this real-time data. Additionally, the CMMS’s reporting features provide comprehensive information on maintenance costs, trends, and frequencies. This analytical method enhances overall asset management strategies, optimizes maintenance schedules, and helps find reoccurring issues. CMMS is a vital tool for preserving operational dependability and efficiency because of its powerful reporting capabilities and real-time monitoring.
7. Integration with Other Systems
Contemporary CMMS software frequently has smooth integrations with other enterprise systems, including inventory management systems, Internet of Things devices, and Enterprise Resource Planning (ERP) systems. Data flow between the organization’s various functions is made possible by this integration, which creates a more cohesive operating environment. An ERP system and CMMS integration, for instance, can guarantee that maintenance and production schedules coincide, reducing operational disruptions. Real-time data from IoT devices can be fed into the CMMS, giving predictive maintenance insights. By ensuring that consumables and spare parts are available when needed, inventory management integration helps to minimize maintenance task delays. These integrations improve the maintenance management process’s overall responsiveness and efficiency.
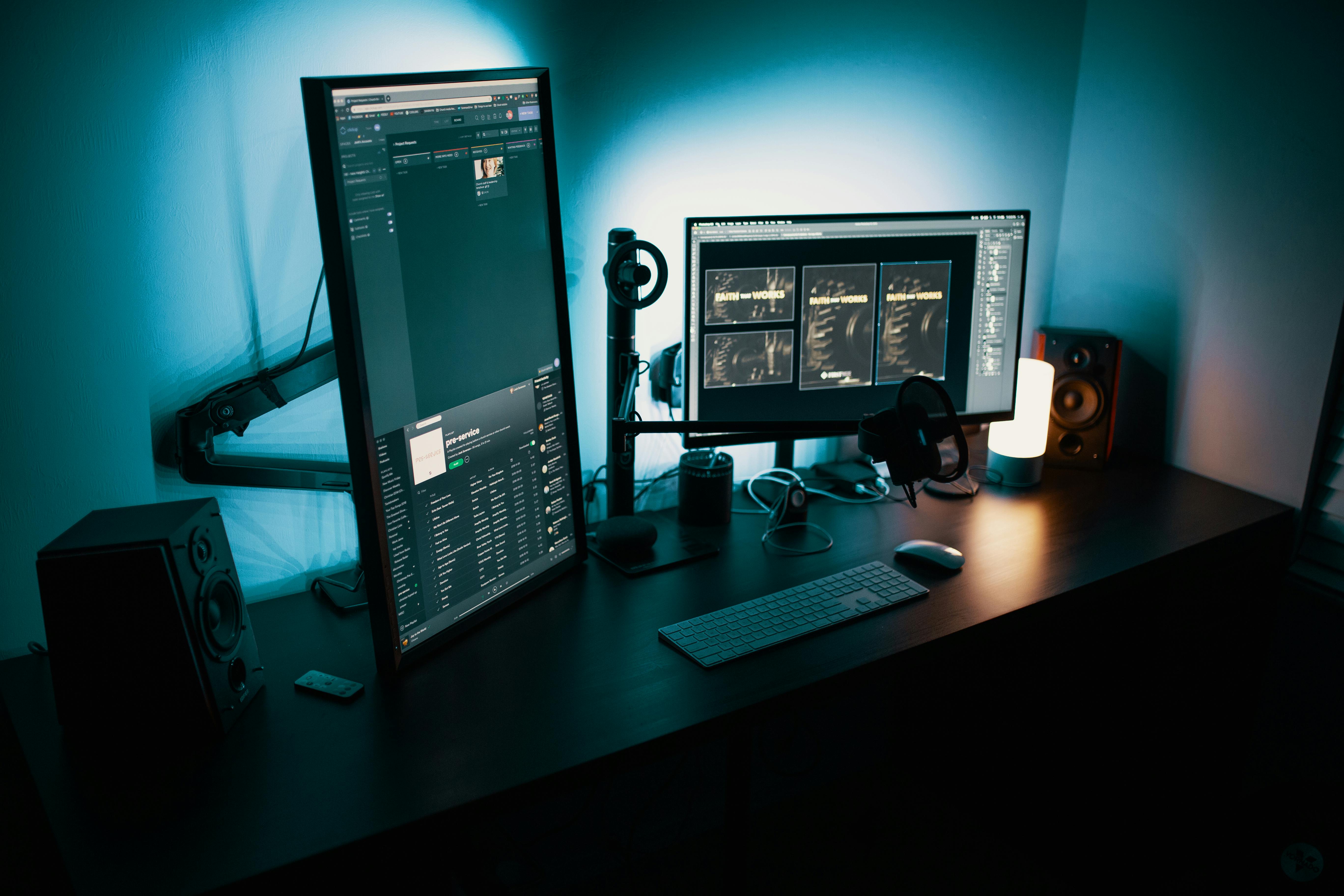
8. Future Trends in CMMS and Preventive Maintenance
Preventive maintenance and CMMS are moving more and more in the direction of increased automation and intelligence. Future CMMS systems will provide predictive analytics that can identify possible problems before they materialize thanks to developments in AI and machine learning. IoT device integration will proliferate, offering real-time data for even more accurate maintenance planning. Accessibility will be further improved by mobile technology, which will enable maintenance teams to enter data and get alerts while on the go. By providing virtual simulations for training and troubleshooting, augmented reality (AR) and virtual reality (VR) technologies may also find their way into CMMS applications. Preventive maintenance will become even more robust and efficient as a result of the ongoing technological advancements, raising the bar for industry standards.